Calculating OEE
OEE (Overall Equipment Effectiveness) offers the gold standard when it comes to measuring manufacturing productivity. When used accurately, it identifies how much of your manufacturing cycle time is productive.
For example, if your OEE score rates 100%, that means you are manufacturing only good parts and doing so as fast as possible, with no stop in cycle time or planned production time.
OEE calculation offers one of the most crucial performance measurements for modern manufacturing facilities.
Being able to optimize your OEE means that you reduce costs, increase capacity and efficiencies, and improve the quality of your planned production time at the maximum possible speed.
What is OEE?
Overall equipment effectiveness is one of the management KPIs that allows you to measure the level of productivity of your assets.
When you calculate OEE, you can combine three components that highlight the level of efficiency an asset you have during manufacturing.
The three main factors are the quality of production, performance, and availability.
Each of these three factors should tell you something different about how your asset operates during the manufacturing process and affect your actual output.
Availability should tell you how often your asset functions when it is needed. Performance highlights how much the asset produces during the manufacturing process. Quality indicates the number of high-quality items your asset produces in the manufacturing line.
As mentioned earlier, if a given asset operates at an OEE calculation score of 100%, that means that every item it produces comes without any defect in quality. It also means that your asset is producing as fast as it should without experiencing any unplanned stops in operating time.
Download our OEE Pocket Guide
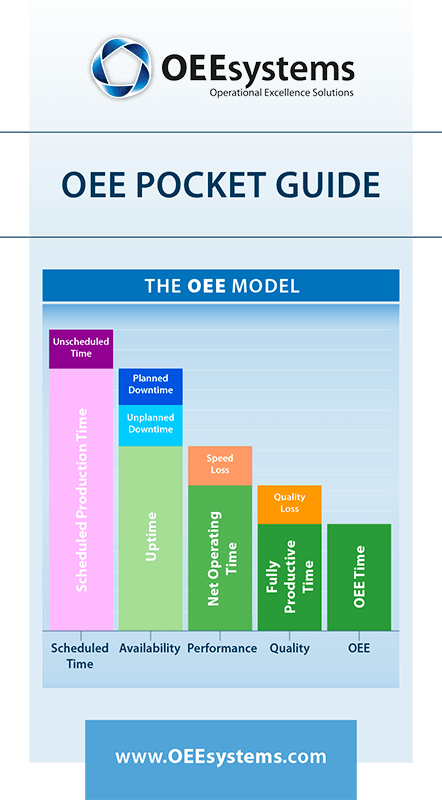
How To Calculate OEE?
So, how is OEE calculated?
The OEE formula involves multiplying performance, availability, and quality, representing your result in a percentage.
The first place to start is to measure the Availability. You can calculate availability simply by dividing the total operating time of your asset by its total planned production time. That does not include expected downtimes, minor stops, holidays, planned shutdowns for maintenance works, or any other similar scenario.
For example, if you expect a machine to run for about 12 hours, but an unexpected breakdown occurs that causes it to run for only 11 hours, your availability will only be 91.7% or 0.917.
Measuring OEE is one of the most important key performance indicators (KPIs) that manufacturing businesses need to pay close attention to. Overall equipment effectiveness is an essential tool for businesses to evaluate the efficiency of their assets throughout any manufacturing process. You can also use OEE to investigate processes, tools, or people that play a role in how your assets operate.
The final thing you should determine is the Quality of goods or items your asset produces. You can calculate the quality by dividing the number of working units you produce by the total units started.
For example, if your asset uses 12 hours to give 12,000 units, with about 300 defects that render them unusable, then your number of functional units will fall to 11,700. That represents a quality score of 97.5% or 0.975.
After calculating the various scores or values for your three main components, you can multiply all three values to determine your OEE. In this case, if the quality is 97.5% or 0.975, performance is 95.8% or 0.958, and your availability score is 91.7% or 0.917, your OEE measurement should be 85.7% or 0.857.
OEE calculation offers several benefits for manufacturing businesses, depending on how well you manage to use the results of your calculation or the insights it offers.
Availability %
The Process's Actual operating time as a percentage of Scheduled operating time. This is often referred to as Uptime or Runtime.
Performance %
Based on Process throughput, Performance is a measure of expected time to produce throughput (Process Capability) compared to Availability time.
Quality %
The total Good Units produced as a percentage of the Throughput. Also referred to as First Pass Yield (FPY).
Availability x Performance x Quality = OEE %
Assume Machine A is a single product machine and is
capable of producing 1,000 units every hour.
In a 16 hour scheduled production day
Machine A is capable of producing 16,000 good units.
On a particular day Machine A recorded downtime of 2 hours
(e.g. equipment breakdown, waiting on materials etc..)
Scheduled Production Time = 16 Hrs
Downtime (planned & unplanned) = 2 Hrs
Available Time (Uptime) = 16 Hrs – 2 Hrs = 14 Hrs
Available Time / Scheduled Time = 14Hrs/16Hrs = 88% Availability
In this example we will record throughput on the equipment/process
as 12,632 units (cycles) for the 14 hrs of Available Time.
Also remember that the machine can produce 1,000 units an hour.
Available Time = 14 Hrs
Machine Capability Rate = 1000 units per hour
Total product produced (Throughput) in Available Time = 12,632 units
Machine Capability Time to produce 12,632 units = 12,632/1,000 = 12.63 Hrs
Machine Capability Time / Availability Time = 12.63Hrs / 14Hrs = 90% Performance
Out of the 12,632 units (cycles), it was found that only 12,000 of the units were deemed good units (i.e. shippable units). The other 632 are accounted as scrapped and/or rework cycles to make shippable.
Performance Time = 12.63 Hrs
Good Units (expressed in Time) = 12,000 units / 1,000 per Hour = 12 Hrs
Good Units (expressed in Time) / Performance Time = 12Hrs / 12.63 Hrs = 95% Quality
Availability x Performance x Quality = 88% x 90% x 95% = 75% OEE
Therefore, there are losses totaling 25% for the day
(equating to 4 production hours lost).
OEE is about looking at the root causes compiling the 25%, and taking corrective action to reduce the losses and increase the OEE %
How Do You Use OEE?
Your overall equipment effectiveness (OEE) formula offers you an excellent indication of just how efficient your manufacturing process is.
You can use it to measure your assets and find out which ones are underperforming. You can also calculate OEE to connect one or all three of your key OEE factors in your manufacturing or production process - quality, performance, and availability.
Once you manage to pinpoint the source of your problem (that is, what is responsible for the underperformance), you can investigate the underlying issues, solve them, and improve the manufacturing or planned production time.
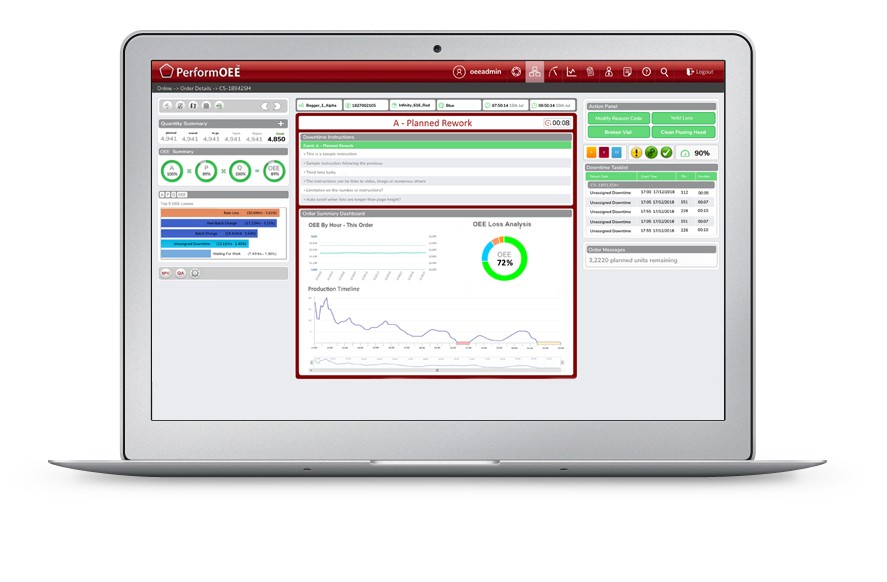
PerformOEE displays detailed and accurate Real-Time A, P, Q & OEE figures calculated automatically from collected data.
A quick colour coded snapshot of your current Top Losses.
Reassignable Downtimes - if needed, the user can augment data retrieved from the machine through this interface.
How is it possible to get the OEE over 100%?
Is it possible for your OEE or any of its underlying metrics to go beyond 100%? It is important to note that the highest rating in calculating OEE or its underlying metrics is 100%. That means when your calculation or analysis scores a 100%, every item that comes from your production line is without defect. It also means that you are manufacturing only good items and that your manufacturing process is also as fast as possible, with no stops or downtime. Downtime or stop time here does not include planned or scheduled stops for maintenance or upgrades. So, is it possible to score over 100% from your OEE calculator? The answer is no, as a 100% score already represents a perfect production process. In most cases, if there is any reason for going beyond the perfect score, it usually results from a wrong definition of the planned production time and manufacturing cycle time.
What Is A Good OEE Score?
As mentioned earlier, the perfect OEE score is 100%. However, it is usually difficult for most businesses to hit a perfect 100% score in every production process. So, what can businesses set as a way of benchmarking progress?
An OEE score of 85% is often considered world-class by most discrete manufacturers. And for most companies, this score represents a reasonable long-term goal for their manufacturing process.
Most experts suggest that generally, any OEE low score below 65% should be considered unacceptable for any manufacturing process.
Scores or values that fall between 65% and 75% can be considered regular in most manufacturing processes. They do not necessarily represent a good score but hardly indicate any cause for alarm - aside from the fact that they show a lot more work needs to be done to improve the score. World-class OEE remains at 85% or even better. And if businesses want to set targets that drive continuous development, they should aim to meet the 85% OEE score or better.
Is OEE A KPI?
Measuring OEE is one of the most important key performance indicators (KPIs) that manufacturing businesses need to pay close attention to. Overall equipment effectiveness is an essential tool for businesses to evaluate the efficiency of their assets throughout any manufacturing process. You can also use OEE to investigate processes, tools, or people that play a role in how your assets operate.
When you manage to successfully combine your OEE indicators with insight from other maintenance metrics, you can identify areas of your operation process to improve in ways that make them more quantifiable when measuring your operational progress. A good OEE isn’t something just nice to have. It can assist your business production sector in visualizing manufacturing equipment loss and put in processes for eliminating waste and identifying quality losses. Your OEE score may not provide insight into the exact causes or reasons for your quality loss, poor performance, or drop in productivity. That is the role of the three key factors - availability, performance, and quality.
However, you may get a good general insight into the entire production process when you can capture how well your production process is doing (with the OEE) and the figures that indicate the nature of your losses (with your availability, performance, and quality scores).
The Implications of OEE Calculations for Productivity Management
When you conduct an OEE performance calculation on your production line, you can give yourself some insight into how your business conducts, organizes, and schedules maintenance tasks. You can also ensure a truly productive manufacturing time by ensuring continuous improvement while you achieve maximum speed. With this information, you should be better equipped to avoid or even prevent critical but common issues regarding your organization or manufacturing performance time, money, as asset costing.
For example, a low asset availability should indicate that your machine is breaking down far too long or too often and is causing unplanned downtime that affects your manufacturing or business in general. That could mean that either your maintenance team isn’t putting the proper preventive maintenance measures in place or that you aren’t making the necessary repairs.
Several issues may be responsible for the low performance of your manufacturing or production. It could even be something as relatively straightforward as reduced speed, not oiling some parts of your machinery enough or regularly. It could also mean that you may be failing to fix or replace certain broken parts.
But whatever the cause is, a poor quality score or quality loss usually results from a lack of standardization and process failures. For instance, if your manufacturing system or machinery isn’t correctly aligned, or you fail to set your gauges accurately from shift to shift, you can expect to experience an increasing number of defects in your manufacturing. And this may lead to an increasing number of defective products.
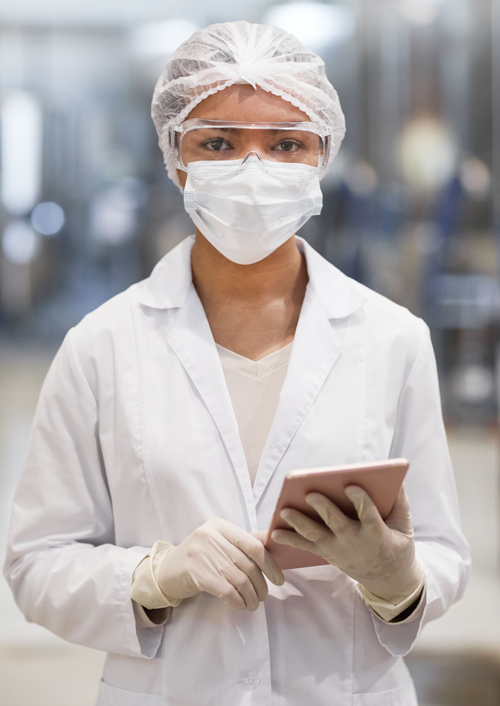
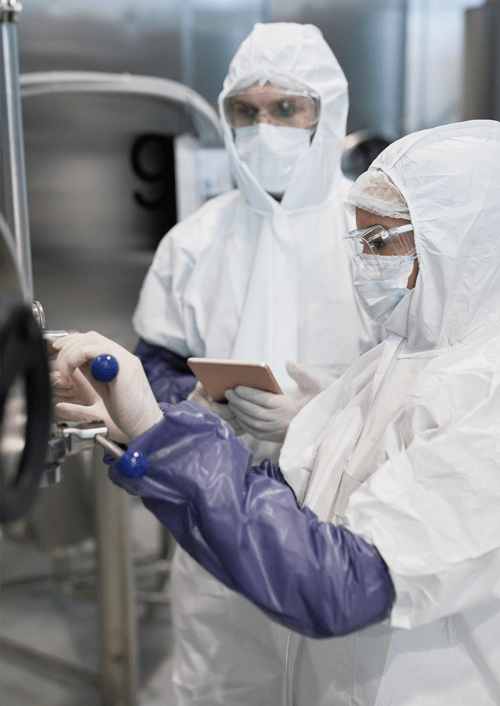
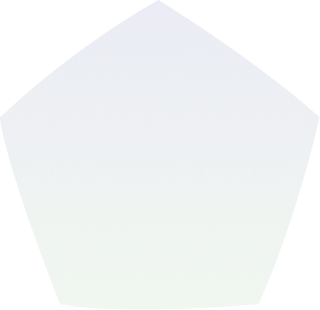
Capterra Client Reviews
Overall Capterra Rating
Take control of your manufacturing operations and drive efficiency with PerformOEE™.
Contact Us Today
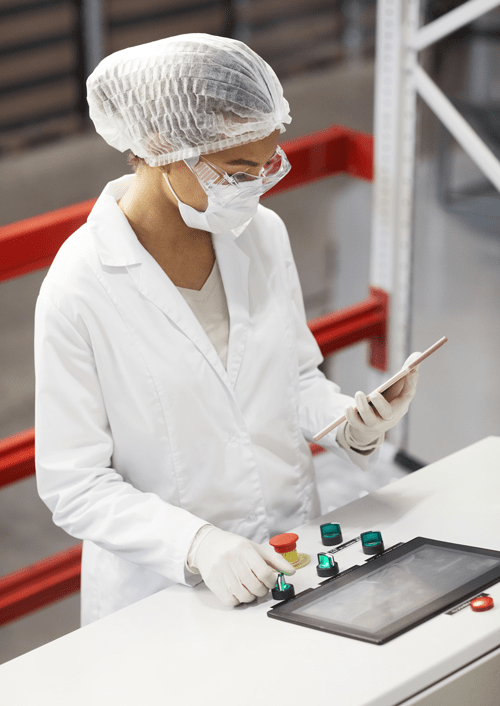